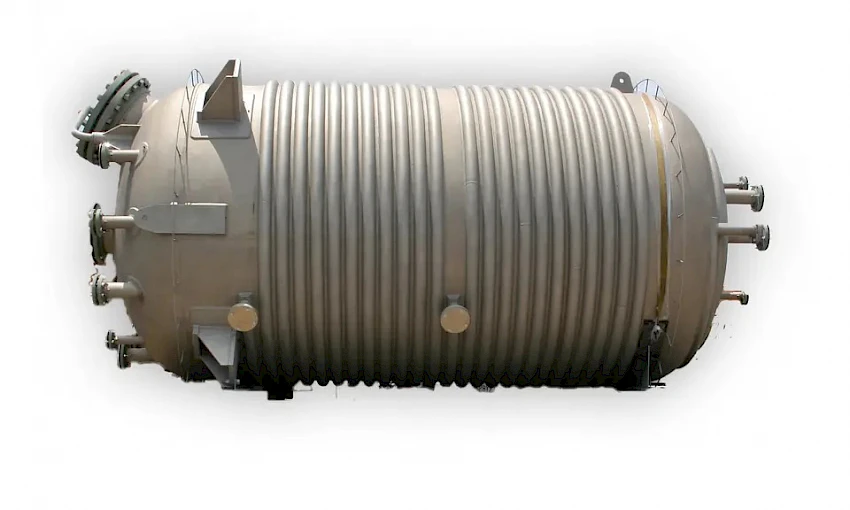
Chemical Reactor: A Comprehensive Guide to Selection, Design, and Optimization
Selecting the right chemical reactor is crucial for achieving efficiency, safety, and optimal performance in your chemical processes. Choosing the wrong reactor can lead to undesirable outcomes, such as poor product quality, safety risks, and operational failures.
At Aces Process, we leverage our expertise to help you choose the reactor that best suits your needs. We consider factors like reaction types, operating conditions, and material properties to ensure the perfect match for your process.
Investing in the right reactor not only provides peace of mind but also boosts your plant's production and profitability. It mitigates risks like poor product quality, safety hazards, and production downtime, setting you up for long-term success.
Partnering with Aces Process offers:
-
Expert Guidance: Our experienced team provides comprehensive support throughout the selection process.
-
Wide Range of Products: We offer a diverse selection of reactors with varying capacities and features to meet your specific needs.
-
Customized Solutions: We provide tailored solutions if standard reactors don't fulfill your requirements.
-
Customer Focus: We prioritize your success and work closely with you to understand your goals.
"Leading companies across various industries worldwide rely on Aces Process Chemical Reactors. For good reason."
If you need a high-quality, customized, and reliable stainless steel reactor, Aces Process is the ideal choice.
Contact us to find the perfect solution for your needs.
Benefits of Choosing the Right Reactor:
-
Higher product quality: Achieve the desired chemical reactions and produce high-quality products.
-
Increased productivity: Optimize your process for faster and more efficient operation, boosting production capacity.
-
Improved safety: Ensure safe operation and reduce risks to personnel and your plant.
-
Lower production costs: Save on energy and raw materials, minimizing production expenses.
Factors to Consider When Choosing a Reactor:
-
Reaction type: The nature of the chemical reaction (exothermic, endothermic, catalytic, etc.) influences reactor selection.
-
Operating conditions: Temperature, pressure, and reactant concentrations impact the choice of reactor.
-
Material properties: Reactor materials must be chemically compatible and suitable for the process conditions.
A Comprehensive Overview of Chemical Reactor Design
Efficient chemical reactor design in the chemical industry relies on the principles of thermodynamics and kinetics. Reactor design involves determining the ideal operating conditions, including:
-
Temperature
-
Pressure
-
Residence time
-
Reactant concentrations
The pressure vessel, a critical component, enables chemical reactions to occur in a safe and controlled environment. Understanding thermodynamics and kinetics helps optimize pressure vessels for maximum efficiency and safety.
Types of Chemical Reactors:
-
Batch Reactors: Process a single batch of materials at a time, suitable for small-scale production or research.
-
Continuous Reactors: Operate at a steady state with continuous input and output, ideal for large-scale production.
The choice between batch and continuous reactors depends on the desired outcome and reaction parameters.
Safety in the Chemical Industry
While the chemical industry is vital for modern life, it presents inherent hazards. Reactor design plays a crucial role in ensuring safety. Key safety considerations include:
-
Pressure relief valves: Prevent overpressure and potential explosions.
-
Containment systems: Mitigate leaks and spills.
-
Emergency shutdown procedures: Enable rapid shutdown in hazardous situations.
By prioritizing safety, the chemical industry can thrive while protecting employees and the public.
Strategic Advantages of Choosing the Right Chemical Reactor:
The right chemical reactor offers significant strategic advantages:
-
Increased Productivity and Profitability: Optimized reactors enhance production rates, efficiency, and profitability.
-
Excellence in Product Quality: Precise control and optimized reaction conditions ensure consistent, high-quality products.
-
Sustainability and Environmental Responsibility: Energy-efficient and low-emission reactors promote sustainability.
-
Technological Innovation: Advanced reactors enable new product development and future-proof your operations.
Factors Affecting Reactor Selection:
-
Reaction Type: The nature of the reaction (exothermic, endothermic, catalytic, etc.) dictates reactor design.
-
Reaction Conditions: Temperature, pressure, pH, and reaction time influence reactor type and size.
-
Properties of Reactants: Reactant concentration, phase (gas, liquid, solid), and chemical properties impact reactor selection.
Types of Chemical Reactors Used in the Chemical Industry:
-
Batch Reactors: Ideal for small-scale production.
-
Continuous Reactors: Suitable for large-scale, continuous production.
-
Other Reactor Types: Volumetric, surface, homogeneous, and heterogeneous reactors cater to specific needs.
Reactor Selection and Optimization:
Choosing the most suitable reactor involves considering various factors, including production capacity, energy efficiency, safety, and environmental impact.
Tips for Optimum Performance:
-
Maintenance and Monitoring: Regular inspections, proper function checks, and thorough cleaning are essential.
-
Regulatory Compliance: Adhere to the latest regulations and industry best practices.
-
Employee Training: Invest in safety training for employees.
-
Technological Advancements: Stay informed about the latest technologies.
By prioritizing maintenance, safety, and continuous improvement, businesses can achieve optimal performance and product quality.
Troubleshooting Common Problems:
Addressing reactor and equipment issues requires expertise, a thorough understanding of chemical processes, and effective problem-solving.
Key Takeaways:
-
Prioritize periodic maintenance and control of reactors.
-
Adhere to safety precautions during chemical processes.
-
Adopt a proactive approach to prevent problems.