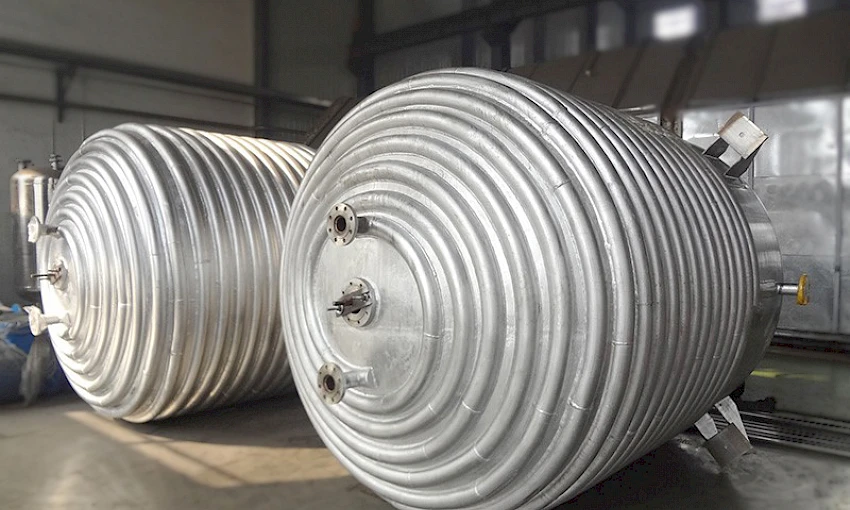
Emulsion Tank Manufacturing
Emulsion tanks are essential equipment in industrial processes, designed to homogeneously mix two or more liquids with different viscosities and create a stable mixture. These tanks are widely used across many sectors and are indispensable in industries like food, cosmetics, pharmaceuticals, chemicals, petroleum, paint, and ink production.
Aces Process is a leader in emulsion tank manufacturing, offering expertise from design to production. Each tank can be customized to meet the unique requirements of the client, ensuring the highest performance and mixture homogeneity.Emulsion tanks provide precise mixing of liquids with varying viscosities, maximizing the quality of the final product.
Emulsion Tank Components
Emulsion tanks consist of the following key components:
-
Tank body: The main body of the tank where the liquids are mixed. The tank body is typically made of stainless steel, carbon steel, or aluminum.
-
Mixer: The equipment that mixes the liquids. Mixers can be blade type, vortex type, or propeller type.
-
Rotation system: The equipment that ensures the mixing and homogenization of the liquids inside the tank. The rotation system can be provided by a pump or a mixer.
-
Heating/cooling system: The equipment used to control the temperature of the liquids. The heating/cooling system can be provided by a steam boiler, a heat exchanger, or a cooling system.
-
Emulsion control system: The equipment used to control the stability of the emulsion. The emulsion control system can be provided by a viscometer, a centrifuge, or an optical sensor.
Emulsion Tank Design
The design of an emulsion tank varies depending on the application area and process requirements. The size, capacity,mixer type, heating/cooling system, and emulsion control system of the tank are selected based on the application.
Emulsion Tank Manufacturing
The emulsion tank body and other components are joined using the appropriate welding method.
Emulsion Tank Tests
Emulsion tanks must undergo various tests after manufacturing. These tests are used to evaluate the performance and durability of the tank.
-
Performance tests: These tests evaluate the tank's ability to mix and homogenize liquids.
-
Durability tests: These tests evaluate the tank's resistance to pressure, wear, and corrosion.
Emulsion Tank Technical Specifications
Emulsion tanks are equipment where two or more liquids are homogeneously mixed to form a stable mixture. These tanks are widely used in industrial applications and are of great importance, especially in sectors such as food, cosmetics,pharmaceuticals, chemicals, petroleum, paint, and ink production.
Aces Process is a pioneer in engineering, determining emulsion tank technical specifications and meeting application requirements. The design of each tank is customized according to the properties of the materials to be processed, the processing volume, and the sensitivity of the application.
Emulsion Tank Technical Specifications
Emulsion tank technical specifications are based on the following key factors:
-
Material: Emulsion tanks are manufactured from different materials depending on the chemical compatibility and temperature tolerance of the liquids to be processed. Materials such as stainless steel, carbon steel, aluminum, or glass are used.
-
Capacity: The size and capacity of the tank are determined according to the amount of material to be processed and the scale of the application. Emulsion tanks are available in various capacities, from laboratory sizes to industrial-scale facilities.
-
Mixing System: Different mixing systems are used for the homogeneous mixing of the emulsion. High-speed rotor-stator mixers are commonly preferred in such processes.
-
Motor Power: The motor power required to operate the mixers is selected depending on the size of the tank and the viscosity of the liquid.
-
Sensors and Control Systems: Sensors and automation systems are used to monitor and control temperature,pressure, level, and other critical parameters during the process.
-
Ease of Cleaning and Maintenance: Emulsion tanks are designed to meet cleaning and maintenance requirements,which increases production efficiency.
Aces Process's Engineering Expertise
Aces Process emphasizes its engineering expertise in meticulously determining emulsion tank technical specifications and designing these tanks to provide the highest level of performance. We offer our customers customized, reliable, and high-quality emulsion tanks. This is designed to best meet the mixing needs in industrial production.
Industrial Applications of Emulsion Tanks
Emulsion tanks are used in various applications across numerous industrial sectors. Here are some of the main sectors where emulsion tanks are utilized:
-
Food and Beverage Industry: Emulsion tanks are widely used in the production of food products. For example,they are used in processes such as the preparation of milk and oil emulsions, chocolate making, mayonnaise production, and the creation of emulsions in creams and sauces.
-
Cosmetics and Personal Care: Emulsion tanks are used in the production of cosmetic products, lotions, creams,and makeup materials. These tanks ensure the homogeneous mixing of oil and water-based substances.
-
Pharmaceutical Industry: Emulsion tanks are used in the production of medicines, vaccines, and other health products. These facilities ensure the homogeneous mixing, stabilization, and quality control of medicines.
-
Chemical Industry: The chemical industry requires the mixing, emulsification, and reaction of different chemical substances. Emulsion tanks are used to ensure the control and safety of chemical processes.
-
Oil and Gas Industry: In the oil and gas industry, emulsion tanks are used to separate water and oil during the processing and refining of crude oil. This is critical to increasing efficiency in energy production.
-
Paint and Coating Industry: The production of paint, varnish, ink, and coating products requires the mixing of color pigments and binders, and emulsion tanks are needed to achieve the desired viscosity and consistency.
-
Textile Industry: In the textile sector, emulsion tanks are used in fabric dyeing, washing, and processing operations. Emulsions are required for applying and fixing dyes to fabrics.
-
Paper and Pulp Industry: Emulsion tanks are used for mixing and processing chemicals in paper production. In this sector, it is important to improve the quality of paper products.
Customizability of Emulsion Tanks
Emulsion tanks are specially designed and configured to meet the unique requirements of each sector. For example,emulsion tanks used in the food and beverage industry must be hygienic and easy to clean. Emulsion tanks used in the cosmetic industry must be designed to work with sensitive materials. Emulsion tanks used in the pharmaceutical industry must meet high quality and safety standards.
At Aces Process, we utilize our engineering expertise and experience to offer our customers the best emulsion tanks in every sector. This plays a critical role in achieving homogeneous mixtures, ensuring product quality, and efficiently managing production processes.
What is an Emulsion Tank?
Emulsion tanks are industrial equipment that enables the efficient mixing of different liquids and the creation of a stable emulsion. They are generally used to make a homogeneous mixture of two or more liquids that do not normally mix.Emulsion tanks bring together components with different densities, viscosities, and chemical properties, ensuring that the final product has the desired quality and stability.