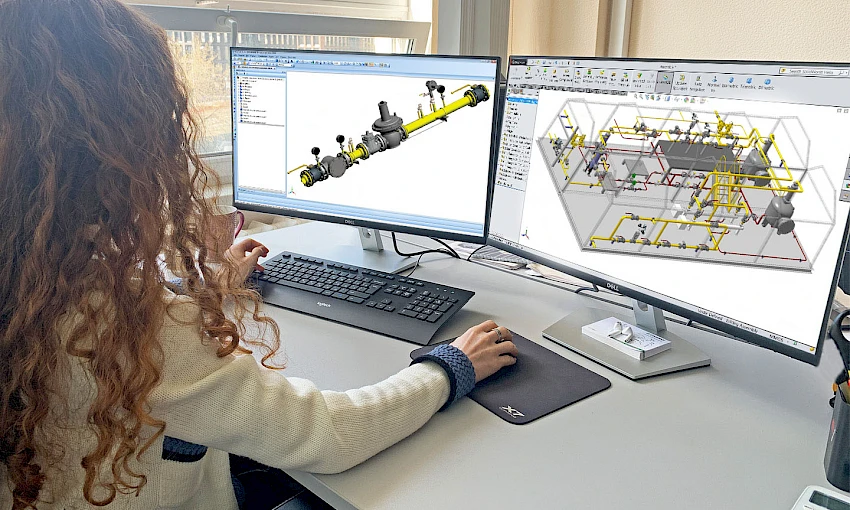
Burner Gas Combustion Line: Design, Manufacturing, and Control
A burner gas combustion line is a system used in industrial and commercial heating, power generation, and process applications. These lines ensure the safe and efficient delivery of gas to the burner and control the gas pressure and flow required for the combustion process. The design, manufacturing, and control of burner gas combustion lines require strict adherence to engineering principles and standards.
Design The design of a gas combustion line forms the foundation of a successful and reliable combustion process. During the design phase, factors such as gas type, flow rate, pressure drop, heating value, and combustion efficiency must be considered. The correct selection of pipe diameter, material, and length is crucial for ensuring low pressure drop, adequate mixing, and combustion control. Safety, ease of operation, and energy efficiency should also be considered during the design process.
Manufacturing The manufacturing of a burner gas combustion line must be carried out in accordance with high-quality standards. This includes selecting suitable materials, proper welding processes, leak testing, and assembly in accordance with standards. During the manufacturing process, full compliance with engineering drawings and specifications must be ensured. The durability of the line, minimizing the risk of gas leaks, and ensuring long-term use are essential.
Control The control of a burner gas combustion line is critical for safety and performance. Leak tests should be performed before and after the installation of the line, and it should be ensured that gas pressure regulators, solenoid valves, and other control elements are functioning properly. In addition, parameters such as gas pressures, flow rates, and combustion efficiency should be monitored regularly and adjusted as needed. The control process should include periodic maintenance and inspections to ensure the safe and efficient operation of the system.
With the right design, quality manufacturing, and regular control, a burner gas combustion line can operate reliably and efficiently. Therefore, it is important to work with a team of expert engineers for the design, manufacturing, and control of these lines. Burner gas combustion lines designed and manufactured in accordance with engineering principles and standards increase energy efficiency, reduce operating costs, and provide a safe working environment.
Key Terms and Definitions:
-
Gas control line: A system that ensures the safe and controlled delivery of gas.
-
Burners: Devices that deliver gas at the correct pressure, flow, and mixture to burners for heating, power generation, or process applications.
-
Gas control system: A system that ensures the safe management of gas. This system includes functions such as controlling gas sources, regulating gas pressure, directing gas flow, and implementing safety measures.
-
Burner gas valve: A type of valve used to control gas flow in a burner system. It controls the opening, closing, or regulation of gas flow to manage the combustion process.
-
Gas pressurestat: A device that automatically opens or closes the gas source when it detects a decrease or increase in gas pressure. This ensures that the correct gas pressure is maintained continuously and ensures safety and efficiency in the system.
-
Gas fitting: A device used to control and direct gas flow. It includes valves, control elements, and fittings used to open, close, or regulate gas sources.
-
Gas filter: A device used in gas systems to trap solid particles, contaminants, or other foreign substances in the gas before it passes through the system. This cleans the gas, protects the system's devices and components, and ensures a safer and more efficient operating environment. Gas filters are typically used before the gas source or at specific points within the gas system.