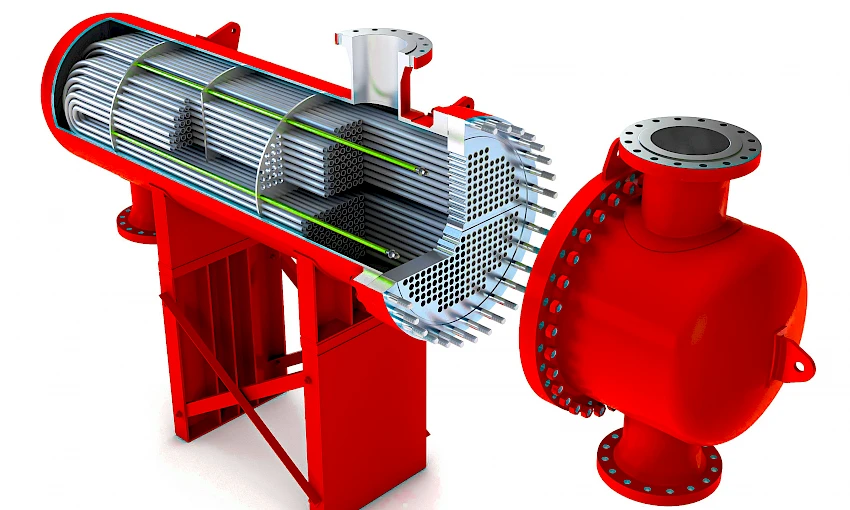
Shell and Tube Heat Exchanger Manufacturing by Aces Process
Aces Process is a recognized leader in the design, fabrication, and supply of high-performance shell and tube heat exchangers. We leverage cutting-edge technology and engineering expertise to provide innovative solutions that optimize heat transfer efficiency across various industrial applications.
What are Shell and Tube Heat Exchangers?
Shell and tube heat exchangers are versatile heat transfer devices widely used in various industries to efficiently exchange thermal energy between two fluids. They consist of a cylindrical shell housing a bundle of tubes through which one fluid flows, while the other fluid flows around the tubes within the shell.
Types of Shell and Tube Heat Exchangers
Shell and tube heat exchangers come in various configurations to cater to diverse industrial needs. Here are some of the common types offered by Aces Process:
1. U-Tube Heat Exchangers:
-
Features: U-shaped tubes fixed to a single tubesheet, allowing for thermal expansion and contraction.
-
Advantages: Simple design, lower cost, easy cleaning of the shell side.
-
Limitations: Difficult to clean the tube side, limited to low-pressure applications.
-
Suitable for: Applications with moderate temperature and pressure differences and where frequent cleaning of the tube side is not required.
2. Straight Tube Heat Exchangers:
-
Features: Straight tubes fixed to two tubesheets at both ends.
-
Advantages: Easy cleaning and maintenance of both shell and tube sides, suitable for high-pressure applications.
-
Limitations: Requires expansion joints to accommodate thermal expansion, higher cost compared to U-tube exchangers.
-
Suitable for: High-pressure and high-temperature applications, where frequent cleaning and maintenance are necessary.
3. Single-Pass, Double-Pass, and Multi-Pass Heat Exchangers:
-
Features: Based on the number of times the tube-side fluid passes through the shell.
-
Single-Pass: Tube-side fluid flows through the shell only once.
-
Double-Pass: Tube-side fluid makes two passes through the shell.
-
Multi-Pass: Tube-side fluid makes multiple passes through the shell.
-
Advantages: Multi-pass configurations increase heat transfer efficiency.
-
Suitable for: Applications requiring varying levels of heat transfer efficiency.
4. Cylindrical and Rectangular Shell Heat Exchangers:
-
Features: Shell shape can be either cylindrical or rectangular.
-
Cylindrical: More common, suitable for high-pressure applications.
-
Rectangular: Offers a larger surface area for heat transfer in a compact space.
-
Suitable for: Applications with specific space constraints or requiring a larger heat transfer surface area.
5. Material-Based Classification:
-
Carbon Steel: Cost-effective and suitable for non-corrosive applications.
-
Stainless Steel: Offers excellent corrosion resistance, suitable for a wide range of applications.
-
Titanium: Highly resistant to corrosion, ideal for harsh environments and corrosive fluids.
-
Other Materials: Depending on specific requirements, heat exchangers can be manufactured from other materials like copper, nickel alloys, or Hastelloy.
At Aces Process, we provide a comprehensive range of shell and tube heat exchangers tailored to your unique needs. Our team of experts can guide you in selecting the optimal type and configuration based on your application, process conditions, and budget. Contact us today to discuss your heat transfer requirements and find the perfect solution.
Advantages of Shell and Tube Heat Exchangers
Shell and tube heat exchangers offer a range of benefits that make them a popular choice across various industries. Here are some of the key advantages:
1. Simple Design & Easy Maintenance
-
Straightforward Construction: The basic structure of a shell and tube heat exchanger is relatively simple, consisting of a shell, tubes, and baffles, making them easy to understand and operate.
-
Accessible for Cleaning and Inspection: Individual tubes can be easily removed for cleaning or replacement without affecting the entire unit, simplifying maintenance and minimizing downtime.
2. Robust & Durable Construction
-
High-Pressure Capability: The robust shell design allows shell and tube heat exchangers to handle high pressures and temperatures, making them suitable for demanding applications.
-
Resistant to Thermal Shock: The ability to withstand sudden temperature changes makes them reliable in processes involving fluctuating temperatures.
-
Long Service Life: With proper maintenance, shell and tube heat exchangers can provide years of dependable service, minimizing replacement costs.
3. High Heat Transfer Efficiency
-
Large Surface Area: The multiple tubes within the shell offer a large surface area for heat transfer, maximizing efficiency.
-
Turbulent Flow: Baffles within the shell create turbulent flow, enhancing heat transfer coefficients and improving overall performance.
-
Multiple Pass Configurations: Options for single, double, or multi-pass configurations further increase heat transfer efficiency by extending the fluid's path and contact time.
4. Wide Operating Range
-
Temperature & Pressure Flexibility: Shell and tube heat exchangers can operate over a broad range of temperatures and pressures, making them adaptable to various process conditions.
-
Suitable for Different Phases: They can handle both liquid and gas phases, expanding their applicability to a wider range of processes.
5. Versatility for Various Fluids
-
Handles Diverse Fluids: They can accommodate various fluids, including corrosive, viscous, and fouling liquids, making them versatile for different industries and applications.
-
Material Compatibility: They can be constructed from a variety of materials, such as carbon steel, stainless steel, titanium, and other alloys, to ensure compatibility with specific fluids and process conditions.
Additional Benefits:
-
Scalability: They can be easily scaled up or down to meet varying capacity requirements.
-
Cost-Effectiveness: Compared to some other heat exchanger types, they offer a cost-effective solution for many applications, especially those requiring high pressures and temperatures.
By offering a combination of simplicity, durability, efficiency, and versatility, shell and tube heat exchangers remain a preferred choice for a wide range of industrial heat transfer needs. At Aces Process, we leverage these advantages to design and manufacture custom heat exchangers that meet your unique requirements and optimize your process efficiency.
Applications of Shell and Tube Heat Exchangers:
-
Oil & Gas Industry: Cooling and heating fluids in refineries, petrochemical plants, and offshore platforms.
-
Chemical Processing: Heat transfer in various chemical reactions, distillation, and condensation processes.
-
Power Generation: Steam generation and condensation in power plants.
-
HVAC Systems: Heating and cooling air and water in commercial and industrial buildings.
-
Food & Beverage Processing: Pasteurization, sterilization, and cooling of various food and beverage products.
Shell and Tube Heat Exchanger Pricing
Understanding the cost factors involved in shell and tube heat exchanger manufacturing helps you make informed decisions when investing in these critical components. Here's a breakdown of the key influences on pricing:
Factors Influencing Pricing:
- Exchanger Capacity & Size:
-
Heat Transfer Area: The primary factor determining the size and capacity of the heat exchanger. Larger surface areas require more materials and fabrication time, leading to higher costs.
-
Flow Rates and Pressure Drops: Higher flow rates or stricter pressure drop requirements may necessitate larger or more complex designs, influencing the overall cost.
- Materials Used:
-
Shell and Tube Materials: Material selection impacts both the cost and performance of the heat exchanger. Exotic materials like titanium or Hastelloy are significantly more expensive than carbon steel but offer superior corrosion resistance.
-
Gaskets and Seals: The choice of gaskets and seals depends on the process fluids and operating conditions. High-temperature or corrosive applications may require more expensive materials, impacting the overall cost.
- Design Complexity:
-
Number of Passes: Multi-pass configurations offer higher heat transfer efficiency but increase complexity and cost.
-
Baffle Type and Arrangement: The type and arrangement of baffles affect fluid flow patterns and heat transfer efficiency. Complex baffle designs may increase manufacturing costs.
-
Nozzles and Connections: The number, size, and location of nozzles and connections can impact fabrication complexity and cost.
Additional Cost Factors:
-
Customization: Custom-designed heat exchangers tailored to specific applications may incur additional engineering and manufacturing costs.
-
Surface Finishes: Special surface finishes, such as electropolishing or glass lining, can improve performance and corrosion resistance but add to the overall cost.
-
Testing and Certification: Rigorous testing and certification to industry standards may involve additional expenses.
-
Delivery and Installation: Logistics and installation costs can vary depending on the size and location of the project.
Get a Quote from Aces Process:
At Aces Process, we provide transparent and competitive pricing for our shell and tube heat exchangers. To receive an accurate quote, we'll need to gather information on your specific requirements, including:
-
Process Conditions: Flow rates, temperatures, pressures, and fluid properties.
-
Desired Heat Transfer: Required heat duty and allowable temperature differences.
-
Material Selection: Compatible materials for the shell, tubes, and gaskets based on the process fluids.
-
Design Preferences: Number of passes, baffle type, nozzle configuration, and other design considerations.
Contact us today for a personalized consultation and quote for your shell and tube heat exchanger needs. We're committed to providing cost-effective solutions that optimize your process efficiency and maximize your return on investment.
Heat Exchanger Maintenance & Cleaning
Regular maintenance and cleaning of your heat exchanger are critical to ensure optimal performance, extend its lifespan,and prevent costly downtime. Aces Process offers comprehensive services to keep your heat exchangers in prime condition, maximizing their efficiency and reliability.
Importance of Heat Exchanger Maintenance & Cleaning:
-
Prevents Fouling: Over time, deposits and contaminants build up on heat transfer surfaces, impeding heat exchange and reducing efficiency. Regular cleaning prevents fouling and maintains optimal performance.
-
Maximizes Energy Efficiency: A clean heat exchanger operates at its peak efficiency, minimizing energy consumption and operating costs.
-
Extends Equipment Lifespan: Regular maintenance and cleaning prevent corrosion, wear, and damage, extending the lifespan of your heat exchanger and reducing the need for premature replacement.
-
Ensures Process Reliability: By preventing fouling and maintaining optimal performance, regular maintenance helps avoid unexpected shutdowns and disruptions to your processes.
Our Professional Maintenance & Cleaning Services:
-
Inspection & Assessment: We conduct thorough inspections to identify signs of fouling, corrosion, or damage,assessing the overall condition of your heat exchanger.
-
Cleaning: We employ appropriate cleaning methods, such as chemical cleaning, mechanical cleaning, or hydro jetting, tailored to your specific heat exchanger type and fouling conditions.
-
Maintenance: We perform routine maintenance tasks, including gasket replacement, tube bundle inspection, and leak detection, to ensure proper functioning and prevent potential issues.
-
Performance Optimization: We optimize the performance of your heat exchanger through adjustments and fine-tuning, ensuring maximum efficiency and heat transfer.
Why Choose Aces Process?
-
Expertise: Our experienced technicians possess in-depth knowledge of various heat exchanger types and cleaning methods, ensuring effective and safe cleaning processes.
-
Customized Solutions: We tailor our maintenance and cleaning plans to your specific needs and operating conditions, optimizing performance and minimizing downtime.
-
Quality Assurance: We use high-quality cleaning agents and equipment, adhering to industry standards and best practices to ensure thorough cleaning and prevent damage to your equipment.
-
Preventative Maintenance: We offer proactive maintenance programs to identify potential issues early and prevent costly breakdowns, ensuring the longevity and reliability of your heat exchanger.
Keep Your Heat Exchanger in Top Condition with Aces Process
Trust Aces Process to keep your heat exchanger operating at its peak performance. Our professional maintenance and cleaning services will maximize efficiency, extend equipment lifespan, and minimize downtime, contributing to the overall success of your operations. Contact us today to schedule a consultation and learn more about our comprehensive heat exchanger maintenance and cleaning solutions.
Heat Exchanger Strength Testing at Aces Process
At Aces Process, we prioritize the safety and reliability of our heat exchangers. That's why we subject every unit to rigorous strength testing, including hydrostatic testing, to ensure its structural integrity and leak-tightness before it leaves our facility.
Hydrostatic Testing:
This essential test involves filling the heat exchanger with water and pressurizing it to a specified level, exceeding its normal operating pressure. This simulates extreme operating conditions and helps identify any potential weaknesses or leaks in the welds, joints, or materials.
Benefits of Hydrostatic Testing:
-
Verifies Structural Integrity: Ensures the heat exchanger can withstand the intended operating pressures without deformation or failure.
-
Detects Leaks: Pinpoints any leaks in the welds, joints, or materials, preventing potential fluid loss or contamination during operation.
-
Ensures Safety: Provides assurance that the heat exchanger will operate safely and reliably, minimizing the risk of accidents or equipment failure.
-
Meets Industry Standards: Hydrostatic testing is a crucial step in complying with industry standards and regulations, such as ASME Boiler and Pressure Vessel Code.
Our Testing Process:
-
Preparation: The heat exchanger is thoroughly cleaned and inspected before testing.
-
Filling & Pressurization: The unit is filled with water and gradually pressurized to the specified test pressure,typically 1.5 times the design pressure.
-
Holding & Inspection: The pressure is held for a predetermined duration while inspectors visually examine the heat exchanger for any signs of leaks, deformation, or other abnormalities.
-
Depressurization & Drainage: The pressure is slowly released, and the water is drained from the heat exchanger.
-
Documentation: A detailed test report is generated, documenting the test procedure, results, and any observations.
Your Assurance of Quality:
Hydrostatic testing is a critical step in our commitment to delivering high-quality, reliable heat exchangers. By subjecting each unit to rigorous testing, we ensure it meets the highest standards of safety and performance, providing you with peace of mind and confidence in your investment.
Contact Aces Process Today:
If you're seeking a reliable partner for your heat exchanger needs, contact Aces Process today. Our expertise in design,manufacturing, and testing guarantees heat exchangers that deliver optimal performance and meet your specific requirements.
Call to Action:
-
Watch our Shell and Tube Heat Exchanger Pressure Test Video!
-
Get in touch for a personalized quote and expert consultation.
Shell and Tube Heat Exchanger Prices: Factors and Considerations
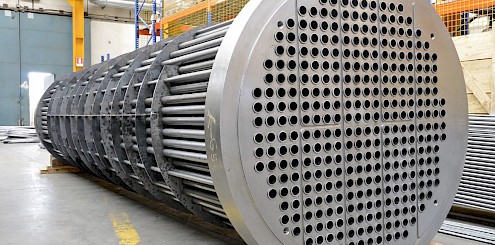
In this article, we will delve into shell and tube heat exchangers that push the boundaries of engineering and explore their limitless potential and unique features.
As ACES engineers, we are inspired by the revolutionary impact of machines in industrial processes and are dedicated to continuously developing new processes and machines to provide lasting support to our customers. We prioritize customer satisfaction, aiming to make our clients more competitive and to be a partner in their success.
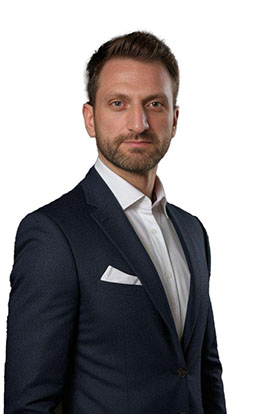
Contact
Phone : +90 536 233 30 76
Email : [email protected]
Address
Address : Ovacık Mah. Mimar Sokak No:10
Başiskele / KOCAELİ / TÜRKİYE