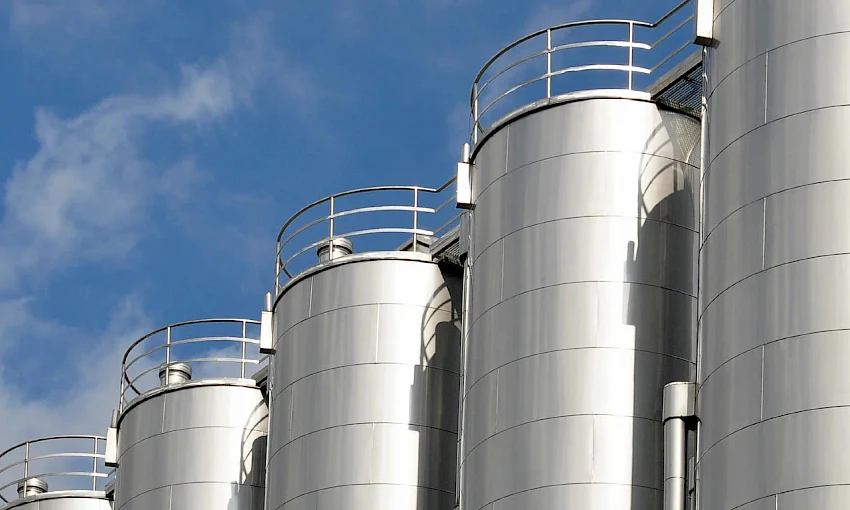
Stainless Steel Tank Design, Manufacturing, and Installation Services
At Aces Process, we take a leading role in the industry by offering a seamless experience that encompasses the design, manufacture, and installation of stainless steel tanks. With our robust engineering infrastructure, experienced team, and meticulous working principles, we provide optimal solutions for every need and condition.
Customized Solutions:
We meticulously analyze the specific requirements of our customers and design stainless steel tanks that meet the unique needs of each project. By considering industrial standards and specific requirements, we ensure that each tank is manufactured in the most suitable way for its intended use and conditions.
Wide Product Range:
We offer a wide range of stainless steel tanks for various needs, including storage, transportation, and processing. Our product range includes pressure tanks, storage tanks, mixing tanks, raw material tanks, reactors, and more.
Engineering Expertise:
At the heart of every project lies a solid engineering foundation and deep knowledge. Our experienced engineers use the latest technology and production techniques to manufacture the highest quality stainless steel tanks.
Advantages of Stainless Steel Tank Manufacturing with Aces Process:
-
Flawless Quality: Manufacturing at the highest quality standards
-
Durability: Long-lasting and robust products
-
Hygiene: Production in hygienic conditions
-
Safety: Compliance with all safety standards
-
Efficiency: Solutions that increase the efficiency of your business
-
Profitability: Investments that provide profitability in the long term
Reasons to Choose Aces Process:
-
Experience and Expertise: We are always there for you with our more than 20 years of experience and expertise in the sector.
-
Customer Focus: We prioritize the needs and satisfaction of our customers above all else.
-
Innovative Solutions: We are in constant pursuit of innovation and use the latest technology and production techniques.
-
Reliability and Quality: Our products and services are offered in accordance with the highest quality standards.
-
Competitive Prices: We offer the highest quality at the most affordable prices.
Do You Need a Stainless Steel Tank?
You can rely on the expertise of Aces Process. We are ready to provide all kinds of support to design, manufacture, and install the most suitable stainless steel tank for your needs.
Frequently Asked Questions about Stainless Steel Tanks:
What is a Stainless Steel Tank?
Stainless steel tanks are special storage and stock tanks made of 304, 316, or 321 stainless steel, used for storing various liquid substances. These tanks are especially preferred in hygienic environments and environments with a risk of rust. Unlike normal steel, stainless steel is resistant to corrosion, which makes it an ideal environment for storing liquids for a long time.
The long-lasting, safe, and durable structure of stainless steel tanks ensures that they find a wide range of uses in industrial facilities. In addition to safely storing powders or liquids, these tanks increase efficiency in processing processes such as mixing, heating, and cooling with additional equipment such as mixers, coils, jackets, and insulation.
Stainless steel tanks are preferred in many areas, from food processing plants to the chemical industry, from the pharmaceutical industry to the energy sector. Thanks to their strong structure, they offer reliable performance for many years and ensure business continuity.
How is Stainless Steel Tank Design Done?
Stainless steel tank design must be done to meet the specific requirements for a particular application. In this article, we present a roadmap of how to design a perfect stainless steel tank in 7 steps.
-
Determining Requirements:
-
What is the application in which the tank will be used?
-
What are the properties of the liquid to be stored?
-
What is the volume, pressure, and temperature range?
-
What are the other operational factors?
-
-
Material Selection:
-
Stainless steel types (304, 316, etc.)
-
Corrosion resistance and temperature resistance
-
Other special requirements
-
-
Sizing and Design:
-
Storage volume and internal pressure calculations
-
Tank shape, base type, and inlet/outlet points
-
Connections, support structures, and other components
-
-
Safety and Standards:
-
Local regulations and industry standards
-
Fire prevention, leak protection, and safety valves
-
Alarm systems and other safety measures
-
-
Support and Configuration:
-
Area where the tank will be placed and support requirements
-
Foundation, platform, or support structures
-
-
Manufacturing and Assembly:
-
Welding processes and quality control
-
Tests and other manufacturing stages
-
Assembly and installation
-
-
Maintenance and Inspection:
-
Regular cleaning and corrosion control
-
Leak tests and preventive maintenance
-
Stainless steel tank design can be a complex process. By following these 7 steps and working with our expert team, you can have a stainless steel tank that fully meets your needs and can be used without any problems for many years.
As Aces Process, we would be happy to assist you in the design and manufacture of stainless steel tanks. Our expert team will guide you every step of the way and work closely with you to produce a perfect tank.
How is Stainless Steel Tank Manufacturing Done?
Stainless steel tank manufacturing is a process that requires careful planning, correct material selection, and precise workmanship. Here is the general manufacturing process of a stainless steel tank in 8 steps:
-
Design: The first step is to understand customer requirements and storage needs and start the design process. At this stage, the dimensions, shape, connection points, support structures, and other details of the tank are determined. During the design phase, safety requirements, local regulations, and industry standards are taken into account.
-
Selection of Material to be Used: Stainless steel tanks are usually made of 304, 316, or 321 stainless steel. The material selection is made depending on the properties of the liquid to be stored, corrosion resistance, and other factors. Choosing the right material is important for the durability and longevity of the tank.
-
Cutting and Shaping: Stainless steel plates are cut to design-appropriate dimensions using cutting equipment and presses. The plates are then shaped and bent or welded to form a cylindrical or rectangular tank shape.
-
Determination of Welding Method: The parts of the stainless steel tank are joined using appropriate welding techniques and procedures. TIG (Tungsten Inert Gas) or MIG (Metal Inert Gas) welding methods are commonly used to provide high-quality weld connections. During the welding process, the leak-proofness and structural integrity of the tank are carefully controlled.
-
Connection Points and Hardware: The tank's inlet and outlet points, valves, fasteners, and other hardware are assembled. At this step, sealing gaskets, clamps, and other fasteners are also placed.
-
Processing and Surface Treatments: The inner surface of the tank is processed smoothly and cleanly. The stainless steel surface undergoes grinding and passivation processes to increase smoothness and make it more resistant to corrosion.
-
Testing and Control: At the end of the manufacturing process, tests and controls are carried out to verify that the tank complies with quality and safety standards. These include leak tests, pressure tests, and other quality control processes.
-
Shipping and Assembly: Completed stainless steel tanks are prepared for shipping and properly assembled at the destination. The assembly process includes the placement of the tank, making connections, and other installation operations.
How is the Installation and Assembly of Stainless Steel Tanks Done?
The installation and assembly of stainless steel tanks, when carried out correctly, ensure that you have a robust and safe storage system. Here is the general assembly process of a stainless steel tank in 7 steps:
-
Preparation: Before assembly, the preparation of the storage area is important. The area should be arranged according to the dimensions of the tank and support requirements. The floor on which the tank will be mounted should be level and solid. Necessary safety precautions should be taken.
-
Checking the Parts: Verify that the parts required for the assembly of the tank are complete and in good condition. Check the parts, take measurements, and make sure they comply with quality control processes.
-
Placement of the Tank: It is important to place the tank in the appropriate place. Support structures should be carefully placed on the base and substructure. Make sure the tank is aligned correctly.
-
Connections: The tank's inlet and outlet points, valves, pipes, and other fasteners must be assembled correctly. Make sure the connections are leak-proof and correctly positioned.
-
Welding and Connections: The welding and connections of the parts of the stainless steel tank should be carried out using appropriate welding techniques and procedures. Controls such as non-destructive testing (NDT) should be carried out when necessary to ensure that the welds are of good quality.
-
Tests and Inspections: After the assembly process, tests and inspections should be carried out to verify that the tank is assembled safely and correctly. These may include leak tests, pressure tests, and other controls.
-
Documents and Operating Instructions: It is important to document the assembly process and prepare operating instructions. This means recording the assembly process and providing instructions for the use, maintenance, and safety of the tank.
What is a Chromium Tank?
A chromium tank is a type of tank that is chrome-plated or made of chromium material. Chromium is a metal known for its high corrosion resistance and chemical resistance properties. Chromium tanks are used in applications such as the storage or processing of aggressive chemicals.
Chrome-plated tanks can be created by applying a chromium layer to the surface of steel or other materials. This coating increases the tank's resistance to corrosion and prevents chemicals from coming into contact with the tank surface.
Industries that Utilize Stainless Steel Tanks
Stainless steel tanks are durable and corrosion-resistant storage systems used across a wide range of industries. Their versatility, hygiene, and ability to withstand harsh conditions make them essential for various applications. Here are some of the key industries where stainless steel tanks play a vital role:
-
Food and Beverage Industry: Stainless steel tanks are indispensable for storing and processing a variety of food and beverage products, including:
-
Milk and dairy products
-
Fruit juices and beverages
-
Wine and beer
-
Edible oils and sauces
-
Sugar solutions and other ingredients
-
Stainless steel's hygienic properties and ease of cleaning make it a preferred material in this industry, ensuring food safety and preventing contamination.
-
Chemical Industry: Stainless steel tanks are essential for the safe storage, mixing, and processing of various chemicals, including:
-
Acids and bases
-
Solvents
-
Paints and coatings
-
Detergents
-
Other corrosive or reactive chemicals
-
The corrosion resistance of stainless steel ensures the integrity of the tanks and prevents leaks or contamination, crucial for maintaining safety and regulatory compliance in the chemical industry.
-
Oil and Gas Industry: Stainless steel tanks are widely used in the oil and gas sector for applications such as:
-
Crude oil storage
-
Refined product storage
-
Gas storage and transportation
-
Petrochemical processing
-
Their durability and ability to withstand high pressures and temperatures make them ideal for the demanding conditions of this industry.
-
Water and Wastewater Treatment: Stainless steel tanks are crucial components in water and wastewater treatment facilities, where they are used for:
-
Storing purified water
-
Filtration and treatment processes
-
Disinfection
-
Wastewater storage and processing
-
The hygienic properties and corrosion resistance of stainless steel ensure the safety and quality of water in these applications.
-
Pharmaceutical Industry: Stainless steel tanks are essential in pharmaceutical manufacturing for:
-
Storing raw materials and active pharmaceutical ingredients (APIs)
-
Mixing and blending pharmaceutical solutions
-
Sterilizing equipment and products
-
The hygienic design and ease of cleaning make stainless steel tanks ideal for maintaining the strict hygiene and quality control standards required in pharmaceutical production.
-
Energy Industry: Stainless steel tanks are used in various energy-related applications, including:
-
Fuel storage in power plants
-
Storage of coolants and other fluids in nuclear facilities
-
Thermal energy storage in solar power systems
-
Their durability and ability to withstand high temperatures and pressures make them suitable for the demanding conditions of the energy sector.
Need a reliable stainless steel tank for your operations?
Contact Aces Process today to discuss your requirements and get a customized quote.