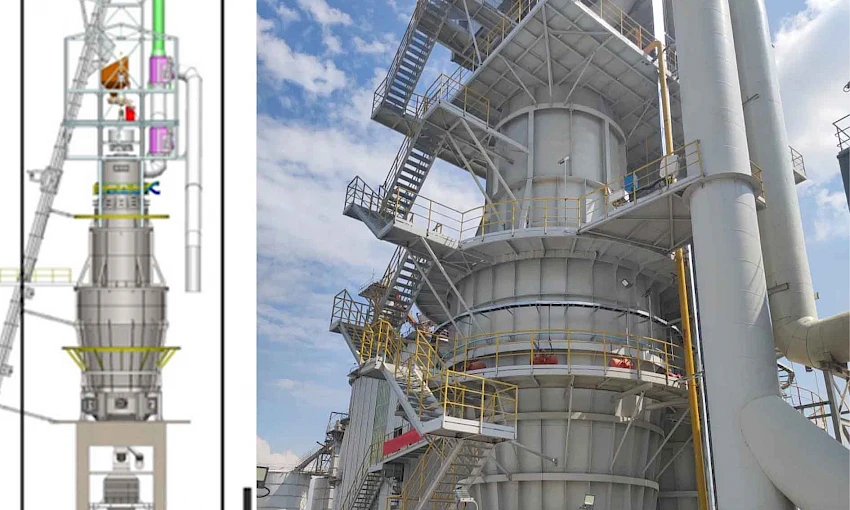
Lime Production Plant – Lime Factory Installation
We offer turnkey installation services for lime production plants, encompassing design, engineering, project planning, manufacturing, installation, and commissioning. We integrally design all processes, from raw material preparation (limestone crushing and screening) to calcination (lime kiln), cooling, storage, dust collection, and automation systems. We establish reliable lime production factories for industries with high-efficiency, environmentally friendly, and customized solutions.
How is Lime Produced?
Lime production is carried out by processing high-purity limestone (calcium carbonate – CaCO₃) extracted from nature at high temperatures. In this process, limestone is heated in calcination kilns at approximately 900–1100°C to remove carbon dioxide, resulting in quicklime (calcium oxide – CaO). If desired, this product can later be reacted with water to obtain hydrated lime (calcium hydroxide – Ca(OH)₂).
The production process primarily consists of the following steps:
-
Raw Material Preparation (Crushing – Screening)
-
Calcination (Kilning)
-
Cooling and Dust Control
-
Product Storage and Packaging
-
(Optional) Hydrated Lime Production
Project Planning and Feasibility in Lime Plants
Planning lime production plants is not just a technical design but also a strategically structured investment process. Plant-specific process requirements, efficiency targets, and time-cost optimization form the basis of the feasibility study.
Process Flow Diagram and Layout Preparation
Each lime plant has a production chain with steps extending from limestone to the final product, hydrated lime. For the efficient operation of this chain:
-
All stages such as raw material preparation, crushing, grinding, kiln feeding, calcination, cooling, dust collection, and packaging are determined.
-
The layout of all units is optimized according to the production flow.
-
Material handling lines, energy lines, maintenance routes, and operational safety areas are planned.
-
Realistic project presentations are prepared with CAD-supported layout plans and 3D modeling.
This ensures that production capacity is maximized and losses in energy, space, and time are prevented.
Detailed Time Planning with Gantt Chart
The success of an investment depends not only on correct project planning but also on accurate time management. During the project process:
-
All stages such as construction, mechanical installation, electrical work, automation, testing, and commissioning are placed on the timeline.
-
Specific start and end dates and the critical path are determined for each work package.
-
Preventive plans and alternative scenarios are developed to avoid delay risks.
-
Work tracking via the Gantt chart provides transparent and effective management for both the investor and the engineering team.
This approach ensures that the investment is commissioned within the planned time and costs associated with delays are prevented.
Capacity and Efficiency Analyses
One of the most important topics for the return on investment and operating profitability is capacity and efficiency analyses. At this stage:
-
Annual, monthly, and hourly lime production targets are calculated.
-
Kiln capacity, raw material consumption, energy consumption, and emission rates are tested with simulations.
-
Ideal equipment selection is made based on capacity balance.
-
Modular capacity increase or multiple product lines (including hydrated lime) are evaluated as options.
-
Energy efficiency is correlated with fuel consumption per ton and the level of automation.
All this data reveals the technical and economic sustainability of the investment decision.
The Importance of Lime in Slag Removal in the Iron and Steel Industry
In the iron and steel sector, lime is an indispensable input for production processes. It is used in many critical processes, especially in blast furnaces for slag formation, removal of steel impurities, gas purification, and wastewater neutralization. Therefore, the supply of high-quality and continuous lime specific to the sector is of great importance for production efficiency.
As Aces Process, we establish high-capacity lime production plants that comply with industry standards, specifically for the iron and steel industry.
-
High-temperature resistant systems
-
Energy-efficient kiln technologies
-
Compliance with ATEX, CE, and ISO standards
-
Environmentally friendly dust control systems
Why is Lime Used in the Iron and Steel Industry?
The slag removal process in iron and steel production is a crucial stage that directly affects product quality. The lime (calcium oxide – CaO) used during this process binds unwanted oxides in molten metals, turning them into slag and allowing them to be removed from the liquid steel.
What are the Basic Components of Lime Factories?
Lime factories are specially designed integrated production facilities for converting limestone into lime. In these facilities, many technical components such as high temperature, reaction control, material handling, and environmental protection work together. The basic components of a lime factory can be categorized under two main headings: Main Facilities and Auxiliary Facilities.
A) Main Facilities
-
Raw Material Preparation Units
-
Limestone crushers
-
Screening systems
-
Feeding bunkers
-
-
Calcination Kilns (Lime Kilns)
-
Shaft type kilns (low capacity and energy efficient)
-
Rotary kilns (high capacity and flexible production)
-
Limestone is heated here between 900–1100°C, and CO₂ gas is separated to obtain CaO (quicklime).
-
-
-
Cooling and Slag Separation Units
-
The produced hot lime is cooled.
-
Dust, stones, and unwanted by-products are separated.
-
-
Hydrated Lime Production Units
-
Quicklime (CaO) reacts with water in a controlled manner to form Ca(OH)₂.
-
Hydrator machines and cooling systems are located in this section.
-
-
Conveying and Conveyor Systems
-
Screw conveyors
-
Bucket elevators
-
Belt conveyor systems
-
-
Storage and Packaging Systems
-
Silos and storage bunkers
-
Big bag filling systems
-
Manual or automatic bagging machines
-
B) Auxiliary Facilities
-
Dust Collection and Filtration Systems
-
Bag filters, cyclones, and stack filters are used to prevent harmful dust from escaping into the environment.
-
Compliance with environmental regulations (EIA, emission limits) is ensured.
-
-
Automation and Control Panels
-
Parameters such as temperature, feed rate, fan speeds, and kiln inclination are automatically controlled by PLC or SCADA systems.
-
Essential for both efficiency and product quality.
-
-
Energy and Fuel Systems
-
Fuels used in kilns: Natural gas, coal, RDF, fuel oil, etc.
-
Heat recovery systems.
-